Plastic extrusion for tubing, profiles, and custom shapes
Plastic extrusion for tubing, profiles, and custom shapes
Blog Article
Understanding the Fundamentals and Applications of Plastic Extrusion in Modern Production
In the realm of contemporary production, the method of plastic extrusion plays a crucial function - plastic extrusion. This intricate procedure, including the melting and shaping of plastic via specialized dies, is leveraged across various markets for the production of diverse products. From vehicle parts to durable goods product packaging, the applications are large, and the capacity for sustainability is equally impressive. Unwinding the principles of this procedure discloses the true flexibility and possibility of plastic extrusion.
The Basics of Plastic Extrusion Refine
While it might show up facility, the principles of the plastic extrusion process are based upon reasonably straightforward concepts. It is a manufacturing process in which plastic is melted and after that formed right into a continuous account via a die. The raw plastic product, usually in the form of pellets, is fed right into an extruder. Inside the extruder, the plastic goes through warmth and stress, causing it to thaw. The liquified plastic is after that required with a shaped opening, referred to as a die, to develop a long, continual item. The extruded product is cooled down and after that reduced to the desired length. The plastic extrusion process is extensively made use of in different industries because of its performance, convenience, and cost-effectiveness.
Different Kinds Of Plastic Extrusion Methods
Structure upon the fundamental understanding of the plastic extrusion procedure, it is essential to discover the numerous techniques associated with this manufacturing approach. The 2 key methods are profile extrusion and sheet extrusion. In profile extrusion, plastic is thawed and created right into a continuous account, typically made use of to produce pipes, poles, rails, and window frames. In comparison, sheet extrusion creates huge, level sheets of plastic, which are generally more refined right into items such as food product packaging, shower curtains, and automobile components. Each strategy needs specialized machinery and exact control over temperature and pressure to ensure the plastic maintains its form during air conditioning. Understanding these strategies is vital to utilizing plastic extrusion efficiently in modern-day manufacturing.
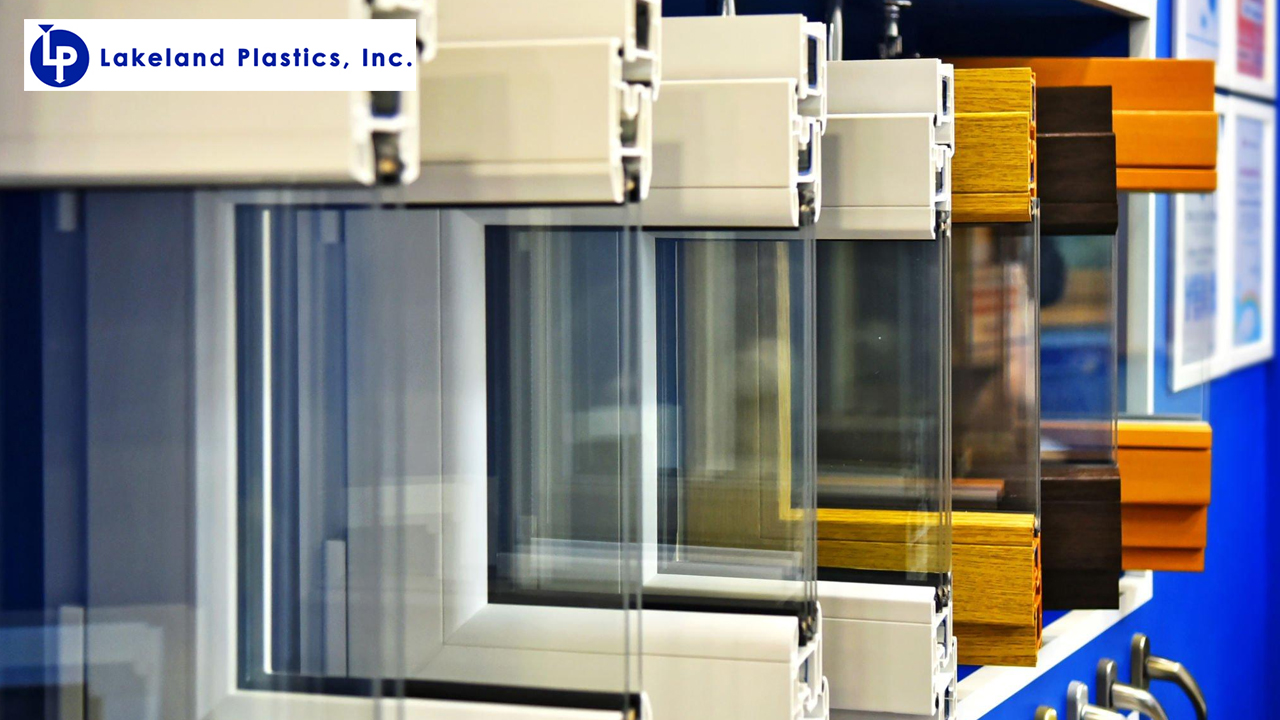
The Role of Plastic Extrusion in the Automotive Industry
A frustrating majority of parts in modern cars are products of the plastic extrusion procedure. This procedure has actually reinvented the vehicle sector, changing it into a much more reliable, economical, and versatile production market. Plastic extrusion is mainly made use of in the manufacturing of read here various vehicle elements such as bumpers, grills, door panels, and control panel trim. The process provides an uniform, regular output, making it possible for producers to generate high-volume parts with excellent accuracy and minimal waste. The lightness of the extruded plastic components adds to the general reduction in vehicle weight, boosting gas effectiveness. Additionally, the toughness and resistance of these parts to heat, chilly, and impact boost the durability of automobiles. Hence, plastic extrusion plays an essential role in auto production.
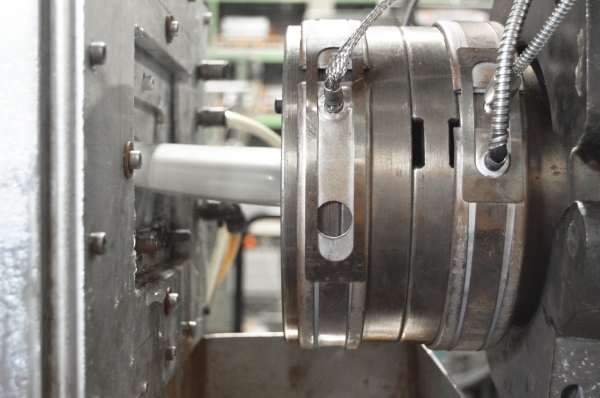
Applications of Plastic Extrusion in Durable Goods Manufacturing
Past its substantial impact on the automobile market, plastic extrusion confirms just as reliable in the realm of consumer goods producing. The adaptability of plastic extrusion permits producers to design and create complex shapes and dimensions with high accuracy and performance. The versatility, adaptability, and cost-effectiveness of plastic extrusion make it a favored choice for numerous consumer products makers, adding dramatically to the sector's development and development.
Environmental Impact and Sustainability in Plastic Extrusion
The pervasive use of plastic extrusion in producing welcomes scrutiny of its environmental implications. Efficient equipment decreases power use, while waste monitoring systems reuse scrap plastic, decreasing raw material demands. Regardless of these renovations, look at this now even more technology is needed to reduce the ecological impact of plastic extrusion.
Final thought
In conclusion, plastic extrusion plays a crucial role in contemporary production, especially in the automobile and customer products sectors. Recognizing the essentials of this process is essential to enhancing its applications and benefits.

The plastic extrusion process is thoroughly used in different sectors due to its efficiency, cost-effectiveness, and versatility.
Building upon the standard understanding of the plastic extrusion process, it is required to discover the different strategies involved in this manufacturing technique. plastic extrusion. In comparison, sheet extrusion develops huge, level sheets of plastic, which are normally additional processed right into items such as food packaging, shower curtains, and cars and truck components.An overwhelming majority of parts in modern-day lorries are products of the plastic useful content extrusion process
Report this page